How lithium-ion battery technology works?
Lithium-ion batteries (LIBs) are the primary power source for various devices, encompassing portable electronics, electric cars, and medical devices. The fundamental working principle involves a sequence of processes facilitating energy storage and release as lithium ions traverse between the anode and cathode of the battery.
The fundamental structure of a lithium-ion battery technology includes crucial elements: an anode, cathode, separator, electrolyte, and two current collectors (positive and negative). The anode and cathode function as storage reservoirs for lithium, while the electrolyte enables the migration of positively charged lithium ions between the anode and cathode. In the charging process, the cathode releases lithium ions, which are then absorbed by the anode. Conversely, the anode releases lithium ions to the cathode during discharge to generate an electric current.
Download PDF Brochure @ https://www.marketsandmarkets.com/pdfdownloadNew.asp?id=49714593
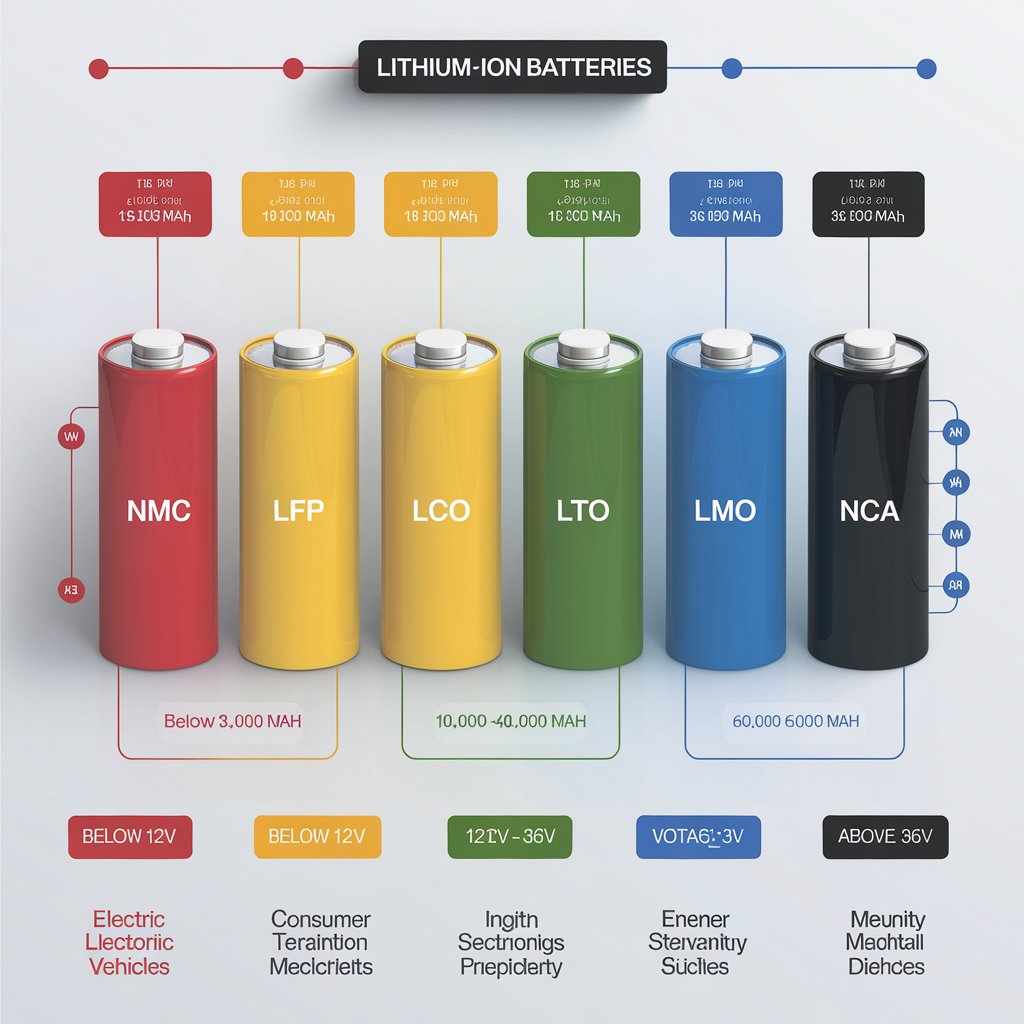
How vital is lithium-ion battery
The lithium-ion battery, a compact and powerful rechargeable battery, has become essential in our everyday work, driving innovations from smartphones to electric cars and energy storage systems. Its role in the digital revolution, electro-mobility, and the transition to green energy is crucial. However, the technology faces challenges as it relies on rare earth metals and other depleting natural resources, raising sustainability concerns. Battery recycling remains a significant challenge.
Future of lithium-ion battery technology
The lithium-ion battery stands out as a pivotal player in the current economic landscape, holding a substantial share of the battery market, particularly in prominent applications like smartphones and electric vehicles. Its dominant market position is attributed to its remarkable energy density and exceptional specifications. Given these advantages, lithium-ion batteries are projected to maintain their significant market presence for the next 5 to 10 years. Despite ongoing efforts by various companies and start-ups to innovate in battery technology, many of these advancements are either partially commercialized or remain in the research and development stage. Technical challenges, such as unsuitable specifications, often hinder the market integration of these innovative batteries.
While some emerging battery technologies show theoretical promise, practical limitations necessitate extensive research and development before being widely adopted. Even if these new technology batteries are commercialized, they find limited applications and are not prevalent in major sectors like smartphones or electric vehicles. Despite lithium-based batteries having certain drawbacks, they are anticipated to remain at the forefront of technology or occupy a substantial market share for a significant period.
Beyond reliable technical specifications, the lithium-ion battery industry boasts a robust logistics infrastructure encompassing mining, transportation, production, battery manufacturing, and machine development. This comprehensive infrastructure underscores the challenge of any alternative battery technology seeking commercialization, particularly for significant applications like smartphones and electric vehicles. The demand for batteries in these applications is predominant, and the existing manufacturing capabilities are well-aligned with their production requirements. Therefore, for a new battery technology to establish dominance in the market, it must offer solutions specifically tailored to these high-demand applications, necessitating a logistics infrastructure akin to that of lithium-ion batteries.
Lithium Extraction and refining
The global economy has witnessed a growing significance of lithium, primarily driven by the demand for energy-efficient electric vehicles and the worldwide initiative towards decarbonization. Various companies are exploring and developing new reserves and refining processes to extract lithium with the highest purity. The extraction and processing of lithium-bearing minerals or brine demand specialized techniques, mainly due to the presence of other mineral salts. Lithium exists in different forms, including lithium minerals and brine. Traditional hard rock mining methods are employed to extract lithium minerals.
In contrast, lithium brine is obtained by pumping underground brine deposits to the surface, where lithium is extracted through a chemical process. Both methods necessitate specialized equipment for efficient extraction. The lithium ore undergoes a refining process upon extraction before being utilized in batteries or other applications. The refining process includes extracting lithium, eliminating impurities, and purifying the substance to create a pure, usable form of lithium. As the demand for lithium-based batteries increases, there is an escalating need for efficient and cost-effective extraction and refining processes. One successful method in producing highly pure lithium crystals is crystallization, which involves the meticulous control of crystal formation and growth. This technology proves essential in the lithium refining industry, ensuring the production of valuable, battery-grade lithium products. Lithium refining emerges as a pivotal process in the entire value chain of lithium, especially when refined for battery-grade applications. The refining business presents a profitable venture with limited players in the industry. Companies engaged in the entire process, from mining to lithium-ion shipping, stand to enhance profitability further.
Lithium availability
Derived from lithium minerals found in the original rock, lithium does not naturally occur in its metallic form due to its highly reactive nature, making it highly flammable and prone to spontaneous reactions with water. Lithium finds applications in various industries, including glass manufacturing, ceramics, pharmaceuticals, batteries, and the production of Aluminum and manganese alloys. Several countries have identified lithium deposits, with some of these identified deposits proving commercially viable.
Recently, the United States Geological Survey (USGS) updated the lithium resources for the United States to 12 million tons and the resources for other countries to 86 million tons. As a result, the total available lithium resource currently stands at approximately 96 million tons.
In recent years, the surge in demand for lithium has been driven by global initiatives to transition from fossil fuels to cleaner energy sources. A key aspect of this transition involves reducing reliance on internal combustion engine vehicles, leading to a notable upswing in the demand for electric vehicles. Consequently, global lithium consumption witnessed a substantial year-on-year increase, surpassing 134,000 tons in 2022, marking a growth of over 40%.
The heightened demand exerted upward pressure on lithium production, which experienced a notable year-on-year boost, reaching 130,000 tons in 2022. However, this production figure still falls short of meeting the annual demand for the metal.
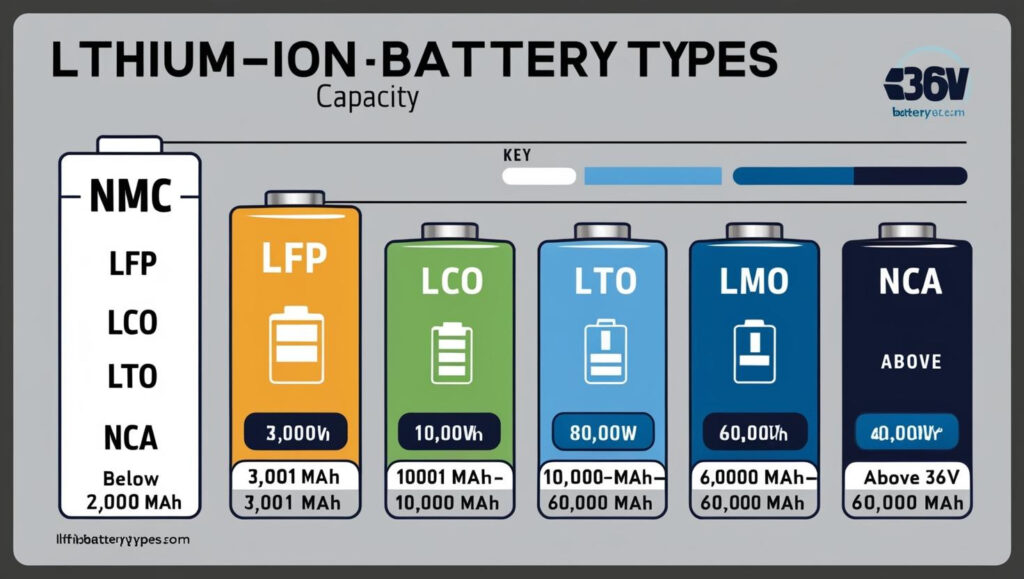
Recycling of lithium-ion battery- How technology helps?
Lithium-ion battery recycling involves the repurposing, reusing, and reprocessing of spent lithium-ion batteries to diminish their disposal as municipal or material waste. As lithium-ion batteries contain various toxic chemicals and heavy metals, disposing of them as regular trash has raised environmental and health concerns, contributing to water pollution and soil contamination. Lithium-ion battery recycling is crucial not only for recovering valuable metals but also for efficient waste management.
A typical battery comprises the cathode, anode, electrode, separator, binder, current collector, and packaging materials. These cell components consist of diverse combinations of materials, including copper, aluminum, nickel, polyethylene, cobalt, nickel, and other chemical compounds. Therefore, the feedstock for lithium-ion battery recycling includes all these components, constituting the spent or end-of-life lithium-ion batteries.
Commonly, used batteries are gathered from electric vehicles, smartphones, laptops, computers, energy storage systems, and other electronic devices. These collected batteries are then sent to battery recycling companies. The recycling process for lithium-air batteries employs various technologies depending on the battery chemistry involved. Critical metals like lithium, nickel, cobalt, magnesium, copper, aluminum, and graphite are extracted from lithium-ion batteries during recycling. The recovered materials are utilized to produce new batteries for various applications.
The construction of lithium battery recycling plants has experienced swift growth. Until November 2022, approximately 44 companies in Canada and the United States and 47 companies in Europe were actively recycling lithium batteries or planning to initiate such recycling operations. Partnerships between automobile companies and battery recyclers were formed to provide the automotive industry with a sustainable source of battery materials.