The aerospace testing industry is undergoing a significant transformation, driven by technological innovations, evolving regulatory requirements, and increasing demand for safer, more efficient, and sustainable air and space transportation systems. As the aerospace sector enters a new era, the testing of complex systems and components is becoming more sophisticated, integrated, and data-driven. From the introduction of artificial intelligence (AI) and machine learning to the expansion of electric and autonomous aircraft, the future of aerospace testing will be marked by advancements that enhance safety, performance, and operational efficiency.
This article explores the key trends shaping the future of the aerospace testing industry, including emerging technologies, evolving industry standards, and the growing role of data analytics in testing processes. We will also examine the diverse types of testing—such as material testing, environmental testing, structural/component testing, and propulsion system testing—as well as their role across commercial, military & defense, and space exploration sectors.
The global aerospace testing market size was valued at USD 5.29 billion in 2024 and is projected to reach USD 6.68 billion by 2029; it is estimated to register a CAGR of 4.8% during the forecast period from 2024 to 2029.
1. Technological Advancements Shaping Aerospace Testing
Artificial Intelligence and Machine Learning
One of the most significant developments in aerospace testing is the increasing use of artificial intelligence (AI) and machine learning (ML). These technologies are revolutionizing how testing is conducted by enabling more intelligent decision-making, automating complex processes, and enhancing predictive capabilities.
Predictive Maintenance and Diagnostics: AI-powered tools can analyze vast amounts of data collected during tests to predict component failures before they occur, thus improving maintenance schedules and extending the lifespan of aerospace systems. ML algorithms can identify patterns in historical test data, helping engineers anticipate potential failures, optimize performance, and reduce downtime.
Automated Testing: Automation is increasingly integrated into aerospace testing processes, including test setup, data collection, and analysis. Machine learning algorithms can automate the interpretation of test results, ensuring that data is processed more quickly and accurately than with manual methods.
Additive Manufacturing and 3D Printing
Additive manufacturing, or 3D printing, is poised to revolutionize aerospace testing, particularly in the development of complex, customized components. The ability to rapidly prototype parts allows for faster iteration of designs and testing of components in real-world scenarios.
Rapid Prototyping: Engineers can use 3D printing to create lightweight, structurally optimized parts and quickly conduct tests. This not only reduces the time and costs associated with manufacturing physical prototypes but also allows for greater design flexibility.
Material Testing: Additive manufacturing also enables the testing of new materials, including lightweight alloys and composites, in a more efficient and cost-effective manner. As aerospace components become increasingly complex, 3D printing will continue to play a critical role in the rapid development and testing of next-generation materials.
Virtual and Augmented Reality for Testing Simulations
Virtual reality (VR) and augmented reality (AR) technologies are becoming more integrated into aerospace testing and design processes. These tools enable engineers to simulate real-world conditions and visualize complex systems in a highly interactive manner.
Design Visualization: Engineers can use VR/AR to conduct virtual “flight tests” or simulate structural behaviors under various environmental conditions without physical testing. This reduces costs and accelerates product development.
Training and Collaboration: These technologies also enhance training by providing immersive environments for testing and simulation, allowing teams to work collaboratively across different locations. This capability is particularly valuable as aerospace systems become more sophisticated and testing becomes increasingly global.
2. Shifting Regulatory Requirements and Standards
As the aerospace industry evolves, so too do the regulatory frameworks governing aerospace testing. Regulatory bodies such as the Federal Aviation Administration (FAA), European Union Aviation Safety Agency (EASA), and International Civil Aviation Organization (ICAO) are introducing new standards to accommodate emerging technologies and address environmental concerns.
Electric and Hybrid Aircraft Testing
With growing interest in electric aviation and hybrid-electric propulsion systems, regulatory agencies are developing new testing protocols for aircraft that rely on electric engines or alternative fuel sources. These innovations present unique challenges in terms of testing battery life, energy efficiency, charging infrastructure, and thermal management systems, all of which are being integrated into new testing standards.
Battery Testing and Certification: The growing reliance on electric propulsion systems requires comprehensive testing of batteries and fuel cells under various operating conditions. This includes testing for thermal stability, charging cycles, and safety during thermal runaway events, all of which must comply with updated regulatory requirements.
Autonomous Aircraft Testing: The development of autonomous or remotely piloted aircraft also introduces new regulatory considerations. Testing for autonomous systems will need to ensure safety in both normal and emergency conditions, including software validation, redundancy checks, and response to real-world variables such as weather and air traffic management.
Environmental Sustainability Regulations
Environmental sustainability is increasingly influencing aerospace testing standards. The aerospace sector faces growing pressure to reduce its carbon footprint and meet stricter environmental regulations. Green aviation technologies, such as alternative fuels and energy-efficient designs, are at the forefront of these efforts.
Fuel Efficiency Testing: New fuel types, including biofuels and synthetic fuels, will need to undergo rigorous testing to meet emission standards and ensure compatibility with existing engine designs.
Noise and Emission Standards: Testing methods will need to evolve to address the growing emphasis on noise reduction and emissions standards, particularly in urban air mobility (UAM) and electric vertical takeoff and landing (eVTOL) aircraft.
3. Key Testing Areas in Aerospace: Material, Environmental, and Component Testing
The future of aerospace testing will continue to focus on core areas essential for the safety, performance, and longevity of aerospace systems. Below, we outline some key categories of testing that will be central to the industry’s evolution.
Material Testing
Materials used in aerospace systems must meet rigorous performance standards under extreme conditions. As materials evolve to meet the demands of modern aircraft, spacecraft, and propulsion systems, testing is essential for validating their properties.
New Alloys and Composites: Advanced composite materials and alloys offer significant weight reductions, which improve fuel efficiency and reduce operational costs. However, testing these new materials for durability, strength, and fatigue resistance is essential to ensure they meet aerospace standards.
Thermal and Corrosion Testing: Aerospace materials must withstand extreme temperatures and potential corrosive environments. Tests such as thermal cycling and salt spray tests are essential for ensuring the longevity and safety of materials used in engines, airframes, and other critical components.
Environmental Testing
Environmental testing simulates the harsh conditions that aerospace systems face during operation, such as extreme temperatures, pressure fluctuations, humidity, and radiation. These tests are critical for ensuring that systems perform reliably and safely.
Temperature and Pressure Testing: Aerospace systems are subjected to extreme temperatures, from the cold of high-altitude flight to the intense heat of engine operation. Testing materials and components under thermal shock, high-temperature endurance, and cryogenic conditions ensures that they will function properly in real-world environments.
Vacuum and Radiation Testing for Space Exploration: Space exploration systems face additional challenges, including exposure to the vacuum of space, cosmic radiation, and micrometeoroid impacts. These tests are critical for the development of spacecraft that can operate in deep space environments.
Structural/Component Testing
Testing the structural integrity of an aircraft or spacecraft is essential to ensure safety and reliability. Engineers conduct static and dynamic tests to determine how components will react to various forces, including aerodynamic stresses, vibrations, and impact loads.
Fatigue Testing: Repeated cycles of stress can cause structural components to fail, so fatigue testing is vital for determining the lifespan of critical components, such as wings, landing gears, and fuselages.
Crashworthiness Testing: Structural testing also involves evaluating how well a system can protect passengers and crew in the event of a crash. This includes testing of energy absorption materials and safety systems like seatbelts, airbags, and fire suppression.
Avionics/Flight & Electronics Testing
As aerospace systems become more digital, testing avionics and electronic components is increasingly important. These systems must be highly reliable and capable of functioning in extreme environments.
Electromagnetic Interference (EMI) Testing: Aircraft avionics must be tested for susceptibility to electromagnetic interference from external sources, such as radar and communication systems, as well as internal electronics.
Software Testing: Autonomous flight systems and flight control software require rigorous testing to ensure they operate safely and reliably, including fail-safes and redundant systems.
Propulsion System Testing
The heart of any aircraft or spacecraft is its propulsion system, and testing these systems for thrust, fuel efficiency, and emission levels is critical. As the industry moves toward more sustainable propulsion solutions, new testing methods will be required.
Engine Performance Testing: This involves evaluating how well engines operate under various conditions, such as altitude, temperature, and speed, to ensure they provide optimal performance throughout the lifespan of the aircraft.
Alternative Propulsion Systems: With growing interest in electric propulsion, hybrid engines, and hydrogen-powered systems, testing these next-generation propulsion systems will require new standards and methodologies.
Download PDF Brochure @ https://www.marketsandmarkets.com/pdfdownloadNew.asp?id=32924426
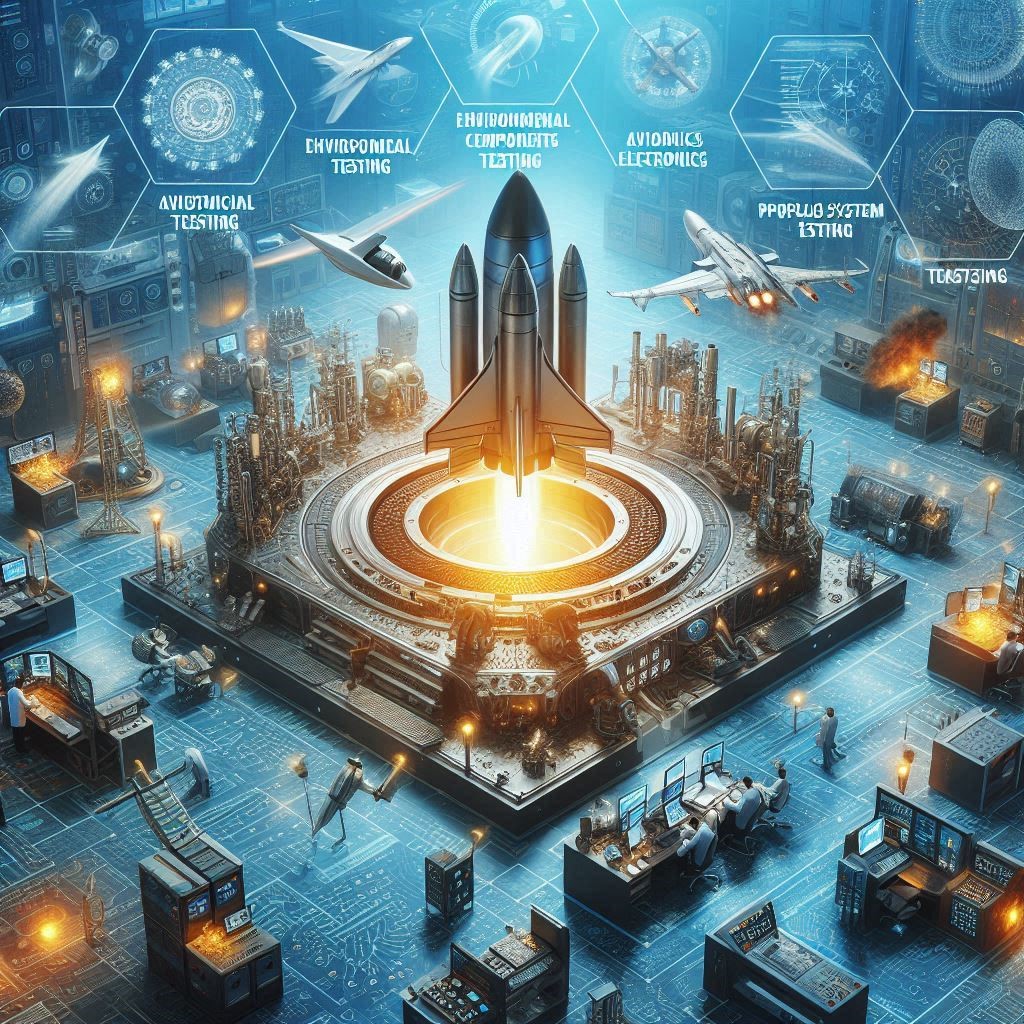
4. Aerospace Testing Across Industries: In-House, Commercial, Military & Defense, and Space Exploration
The future of aerospace testing will involve a wide range of sectors, each with unique requirements for testing aerospace systems.
In-House Testing
Many aerospace manufacturers are establishing in-house testing facilities to streamline their R&D processes. These facilities enable quicker iteration of designs and tests, reducing the dependency on third-party testing services. In-house testing allows for more control over the testing environment, ensuring that proprietary technologies and materials are handled with the highest levels of confidentiality.
Commercial Aerospace Testing
In the commercial sector, testing is driven by the need for reliability, cost-effectiveness, and passenger safety. With the rise of urban air mobility (UAM) and eVTOL aircraft, testing protocols will continue to evolve to accommodate new designs and ensure that they meet stringent safety and performance standards for commercial use.
Military & Defense Testing
Military and defense testing focuses on stealth, survivability, and combat performance. Systems in this sector undergo rigorous testing to ensure they can perform under extreme combat conditions, including high-G maneuvers, radar evasion, and harsh weather environments.
Space Exploration Testing
As space exploration moves beyond low-Earth orbit, new technologies, materials, and testing methods will be required for spacecraft, propulsion systems, and habitats designed for long-duration space missions. Testing for radiation protection, microgravity effects, and deep-space propulsion systems will play a pivotal role in advancing human exploration of the Moon, Mars, and beyond.
The future of the aerospace testing industry is shaped by rapidly advancing technologies, new regulatory frameworks, and an expanding range of testing applications across commercial, military, and space exploration sectors. The development of electric propulsion, autonomous flight systems, and space exploration technologies will continue to drive the need for innovation in testing methodologies. From material testing to propulsion system testing, the aerospace testing industry will play a vital role in ensuring the safety, efficiency, and sustainability of the next generation of aerospace systems.
By embracing cutting-edge technologies like AI, machine learning, additive manufacturing, and automation, the aerospace testing industry will be better equipped to meet the challenges of the future and help drive the aerospace sector toward a new era of innovation.
The major companies in the aerospace testing companies are Element Materials Technology (UK), SGS SA (Switzerland), Intertek Group plc (UK), Applus+ (Spain), TÜV SÜD (Germany), TÜV Rheinland (Germany), TÜV NORD Group (Germany), Rohde & Schwarz (Germany), Eurofins Scientific (Luxembourg), The Boeing Company (US), Airbus (Netherlands), MISTRAS Group (US), Lockheed Martin Corporation (US), Bureau Veritas (France), and DEKRA (Germany). Each of the participating companies has extensive solutions and services, strategic acquisitions, and drive for innovation. Also, the offerings are diversified, with an emphasis on emerging markets, including commercial aviation, military & defense, and even space exploration.
About MarketsandMarkets™
MarketsandMarkets™ is a blue ocean alternative in growth consulting and program management, leveraging a man-machine offering to drive supernormal growth for progressive organizations in the B2B space. We have the widest lens on emerging technologies, making us proficient in co-creating supernormal growth for clients.
The B2B economy is witnessing the emergence of $25 trillion of new revenue streams that are substituting existing revenue streams in this decade alone. We work with clients on growth programs, helping them monetize this $25 trillion opportunity through our service lines – TAM Expansion, Go-to-Market (GTM) Strategy to Execution, Market Share Gain, Account Enablement, and Thought Leadership Marketing. Built on the ’GIVE Growth’ principle, we work with several Forbes Global 2000 B2B companies – helping them stay relevant in a disruptive ecosystem. Our insights and strategies are molded by our industry experts, cutting-edge AI-powered Market Intelligence Cloud, and years of research.
The KnowledgeStore™ (our Market Intelligence Cloud) integrates our research, facilitates an analysis of interconnections through a set of applications, helping clients look at the entire ecosystem and understand the revenue shifts happening in their industry. To find out more, visit www.MarketsandMarkets™.com or follow us on Twitter, LinkedIn and Facebook.
Contact:
Mr. Rohan Salgarkar
MarketsandMarkets™ INC.
630 Dundee Road Suite
430 Northbrook, IL 60062 USA : 1-888-600-6441